Work coordination platform
Designed for the automotive industry
As a leader in innovation, you understand the importance of staying ahead of the curve in the fast-moving automotive 4.0 world. KanBo provides you with the tools to do just that by facilitating smart factory operations, streamlining project management, fostering collaboration and solving complex problems.
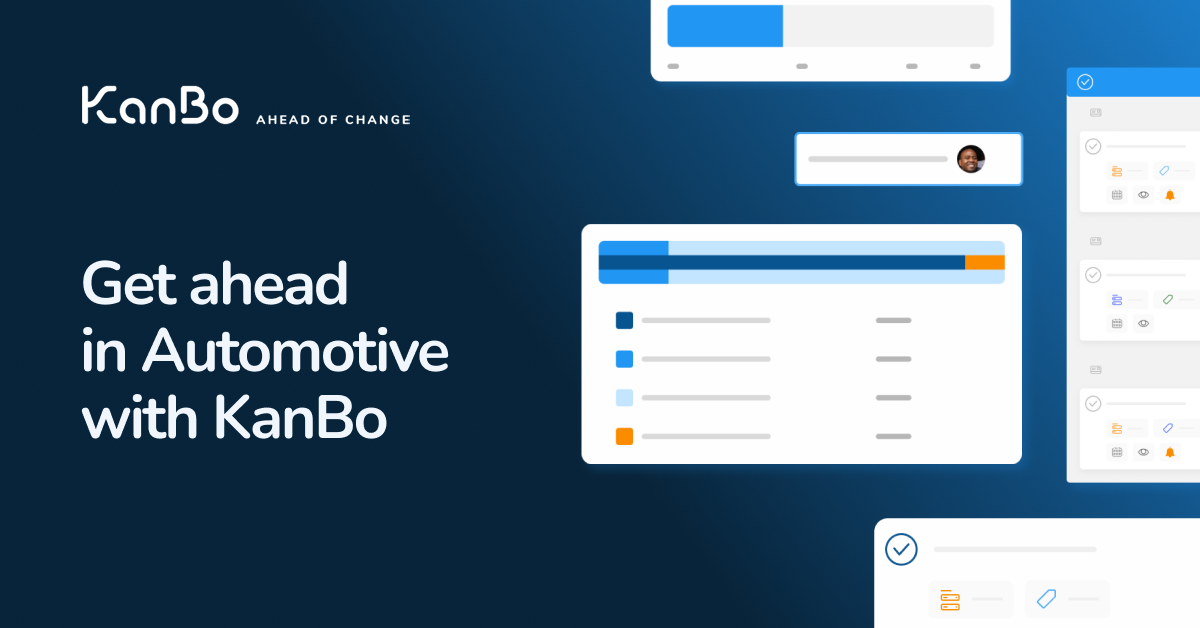
Maximizing Success with Collaboration: How Business Analysts Can Benefit from Effective Collaboration Tools
According to Gartner, “as work becomes more complex and distributed across a team, it’s important to have an effective collaboration platform that enables individuals to work together and share knowledge, as well as monitor progress and provide updates to stakeholders.” KanBo is a collaboration platform that offers just that and more. With its emphasis on collaboration, KanBo helps teams stay connected and work together seamlessly, promoting productivity and success.
In the automotive industry, collaboration is crucial, and a platform such as KanBo can make all the difference. With the industry constantly evolving and facing a myriad of challenges, KanBo provides a one-stop-shop that coordinates, tracks, and manages all aspects of the production and manufacturing processes. It streamlines project management, facilitates smart factory operations, and solves complex problems, allowing companies to stay ahead of the curve in the fast-moving automotive 4.0 world.
KanBo’s integration capabilities also shine in the automotive industry, providing visibility to production lines, suppliers, and logistics networks, enabling teams to work in real-time, collaborate, and communicate more effectively. With the ability to automate routine tasks and the ability to integrate with other enterprise tools, KanBo helps streamline processes, free up time, and minimize errors or missed deadlines.
Furthermore, KanBo’s flexibility encourages the implementation of best practices and standards across departments to create and maintain a continuous improvement loop. This promotes transparency, accountability, and better collaboration among employees, suppliers, and external partners.
KanBo’s dashboard, kanban, and card features help to easily manage each stage of the production and supply chain process by delivering crucial information about inventory, order fulfillment, and performance metrics in a visual format. Teams and stakeholders can easily track progress, identify bottlenecks and take corrective actions before they escalate.
In conclusion, KanBo is a work coordination platform that has been designed with large enterprises in mind, particularly in the automotive industry. Its emphasis on collaboration, flexibility, automation, and integration makes it an indispensable tool for streamlining processes, increasing efficiency, and driving better outcomes.
If you work as a Business Analyst in the Automotive Industry, you know how challenging it can be to keep up with the pace of the industry. That’s why it’s crucial to have a tool that helps you stay organized and collaborate efficiently with your team members. KanBo is the perfect solution for this, and in this how-to guide, we’ll show you how to use KanBo for one week as a Business Analyst in the Automotive Industry.
Monday: Start your week by creating a new Workspace in KanBo for your current project. Invite all the necessary team members to the Workspace and assign roles and responsibilities. Use the Kanban View to visualize your project’s workflow and prioritize tasks.
Tuesday: Collaborate with team members by creating cards for each task and assigning them to the right people. Use Card Elements such as Notes, Checklists, Card Statuses, and Card Blockers to provide essential information and progress updates.
Wednesday: Schedule each card with the appropriate deadlines and reminders, and set up an Activity Stream to receive notifications of any changes or updates. Use the Gantt chart and timeline view to track project progress and ensure that everything is on track.
Thursday: Work on documents directly within KanBo, attaching and detaching them to relevant cards as needed. Use Document Versioning and References to ensure everyone is working on the latest version of all files.
Friday: End your week by reviewing progress and creating reports. Use Dashboards in KanBo to summarize project metrics and visualize project performance. Celebrate your team’s accomplishments and set tasks for the following week.
By following this how-to guide, you can use KanBo to optimize your work as a Business Analyst in the Automotive Industry, collaborate effectively with team members, and keep up with the fast-paced automotive industry.
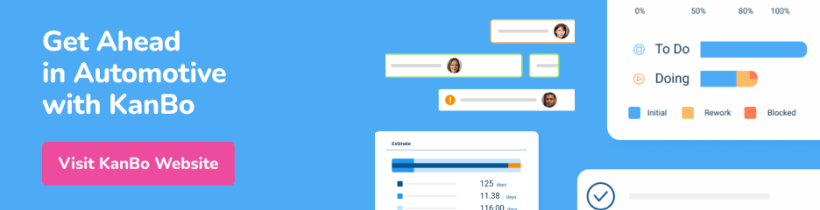
Did you know that KanBo is more than just a tool for collaboration? In fact, KanBo is a complete work coordination platform that goes beyond just collaborating on tasks. With its powerful features, KanBo enables teams to work smarter, faster, and better.
KanBo’s workspaces and spaces provide a dedicated environment for teams to work in. Multiple document sources in spaces make it easy for each team member to access the files they need. KanBo cards are a versatile tool for creating tasks, tracking progress, and managing workflows.
Assigning people to cards and scheduling them ensures that everyone knows what they need to do and when. Card elements such as notes, checklists, and card statuses make it easy to see the progress of a task at a glance. Card blockers help identify issues that need to be resolved before a task can be completed.
KanBo’s document groups and folders make it easy to organize and manage documents related to a project. Document references and versioning ensure that everyone is working with the most up-to-date information.
KanBo’s search functionality makes it easy to find what you need, and comments, notifications, and @mentions allow for easy communication and collaboration between team members.
With KanBo’s visualizations, teams can view their work in kanban, list, table, calendar, Gantt chart, timeline, activity, document, and mind map views depending on what works best for them. Dashboards and reports provide insights into team performance and resource management.
Overall, KanBo is much more than just a collaboration tool. It’s a comprehensive work coordination platform that enables teams to work more efficiently and achieve their goals faster.
Q&A
1. Q: How does KanBo enhance collaboration in the automotive industry?
A: KanBo emphasizes collaboration by allowing teams to stay connected and work together seamlessly, providing a one-stop-shop for coordinating, tracking, and managing all aspects of the production and manufacturing processes. With KanBo, teams can automate routine tasks, have real-time visibility into production lines, suppliers, and logistics networks, and promote transparency and accountability among employees, suppliers, and external partners.
2. Q: How does KanBo help with project management in the automotive industry?
A: KanBo streamlines project management by providing a visual Kanban view to help teams prioritize tasks and visualize the workflow and deadline of each task. KanBo allows team members to collaborate by creating cards for each task and assigning them to the right people, and scheduling cards with the appropriate deadlines and reminders. KanBo helps to track project’s progress and ensures that everything is on track by using the Gantt chart and timeline view.
3. Q: How can KanBo assist with document management in the automotive industry?
A: KanBo assists in document management by allowing teams to work on documents directly within the platform, attaching and detaching files to relevant cards as needed. Users can use Document Versioning and References to ensure that everyone is working on the latest version of all files. By having all documents in one central location, it enables easy access to everyone on the team, eliminates issues with version control, and reduces the time spent searching for documents as all necessary information is embedded within the platform.
Use case: Driving Supplier Assurance Department Performance with KanBo
Supplier Assurance Department plays a critical role in ensuring the timely delivery of high-quality raw materials and components for automotive manufacturing. KanBo can help Supplier Assurance Department collaborate effectively, streamline their workflows, and drive better outcomes.
Performance Measurable and Targets: Use KanBo to monitor supplier performance metrics such as on-time delivery, quality, and cost, and set targets to improve these metrics. KanBo’s data visualization features can help visualize and track performance over time.
Forecast Impact and Monitor Results: Use KanBo to forecast the impact of any changes in supplier performance on the manufacturing process, and monitor the results. KanBo’s automation features can help automate routine tasks such as data entry and reporting, freeing up time for deeper analysis.
Develop Gap Elimination Plans: Use KanBo to identify gaps in supplier performance and develop action plans to close those gaps. KanBo’s task assignment, scheduling, and collaboration features can help ensure that everyone is working towards the same goal.
Training: KanBo can be used to develop and execute training programs for Supplier Assurance Department associates, helping them to understand best practices, standard operating procedures, and tools to improve supplier performance.
Technical Analysis: KanBo can support technical in-depth analysis of current business practices and propose improvement options using its document management and reference features.
Root Cause Analysis: KanBo’s data analysis and collaboration features can help perform deep root cause analysis, engaging with Supplier Assurance Department to understand supplier situation analysis, and work collaboratively to find solutions.
Collaboration with Business Units: Initiate frequent, interactive discussions with other Business Units in order to ensure two-way sharing of thoughts and ideas using KanBo’s collaboration and communication features.
Problem Identification and Countermeasures: Identify problem areas and develop effective countermeasures to correct problems or potentials problems to avoid impacting operations tasks in Automotive Industries using KanBo’s project management features.
KanBo makes collaboration easy by integrating with Microsoft Office, allowing users to use their existing skills to collaborate more efficiently. Users can edit documents stored in KanBo using Microsoft Office applications such as Word, Excel, and PowerPoint. This means that users can continue working on their documents even outside of KanBo.
In conclusion, KanBo can help Supplier Assurance Department in the automotive industry collaborate effectively, streamline their workflows, and achieve better outcomes. With its features in performance tracking, training development, root cause analysis, and Microsoft Office integration, KanBo can help users achieve their goals faster and drive continuous improvement.
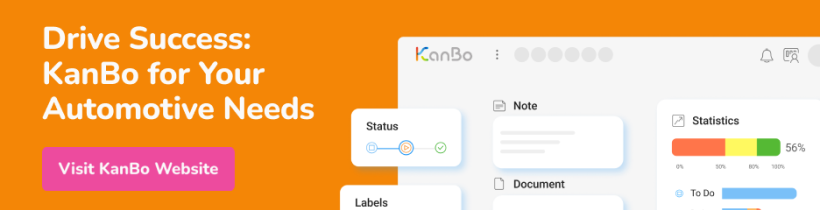