Work coordination platform
Designed for the automotive industry
As a leader in innovation, you understand the importance of staying ahead of the curve in the fast-moving automotive 4.0 world. KanBo provides you with the tools to do just that by facilitating smart factory operations, streamlining project management, fostering collaboration and solving complex problems.
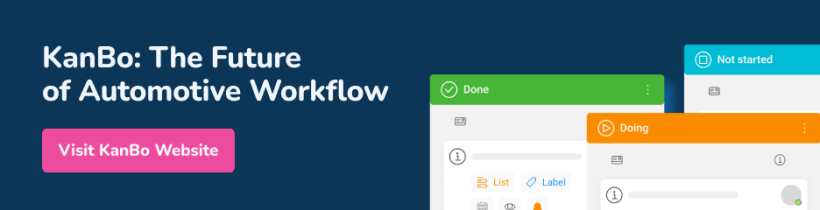
Collaborating for Better Exterior Lighting and Vision Systems: Insights from a Section Chief
Large enterprises often struggle with coordinating the work of multiple teams across various departments. This challenge is especially pressing in the fast-paced, complex world of automotive manufacturing. Recognizing this need, KanBo has developed a work coordination platform designed specifically for large enterprises that prioritizes collaboration and productivity.
KanBo offers a suite of features that enable remote workers to collaborate effectively regardless of their location or time zone. With its easy-to-use interface and intuitive design, KanBo makes it easy for teams to create, share, and track tasks, documents, and projects. The software also offers automation tools, project planning features, and data visualization tools that streamline workflow and improve team productivity.
One of the key benefits of KanBo is its ability to bring all teams, departments, and external stakeholders together on a single platform. This not only simplifies communication processes, but also ensures alignment across different departments, ultimately leading to more successful project outcomes.
KanBo’s strength lies in its ability to cater to the unique needs and preferences of every type of business. The platform can be installed both on-premises and in the cloud, making it a versatile option for enterprises with varying IT infrastructures.
For automotive manufacturers, KanBo provides a collaborative environment that streamlines operations, facilitates smart factory processes, and improves project management. In addition, KanBo also supports technical document creation and ensures compliance with DQS adherence, reducing the risk of errors in specification documents.
Overall, KanBo is a powerful tool for large enterprises looking to maximize collaboration and work coordination across departments and teams. Its ease of use, cloud and on-premises installations, and customizable features make it a must-have for any enterprise looking to stay ahead of the curve in the fast-moving automotive 4.0 industry.
Introduction:
Exterior Lighting and Vision System (ELVS) plays a critical role in the automotive industry as it contributes to the safety and the overall performance of the vehicle. As a Section Chief responsible for ELVS, staying on top of this project is crucial for the success of the department. In this article, we will guide you through a one-week experience of how to utilize KanBo to manage and collaborate on this project.
Monday:
On Monday morning, the Section Chief logs onto KanBo and creates a new workspace for the ELVS project. The workspace contains all the necessary information, such as project goals, timelines, and key stakeholders. The Section Chief proceeds to create a Kanban board with tasks and assigns them to the team members, detailing the priority and due dates.
Tuesday:
On Tuesday, the Section Chief assigns tasks related to sourcing the required materials for ELVS to the Supply Chain team. Using the KanBo template feature, the Section Chief creates a document template with all the information required for the suppliers. Then, the team creates a Document Folder with all ELVS-related documents, which includes all the templates.
Wednesday:
On Wednesday, the Section Chief assigns tasks to the Engineering team to finalize the design of the ELVS. The Engineering team member uploads the latest version of the designs, and the Section Chief approves them, marking the task as “done.” Using the KanBo Card Status feature, the Section Chief can easily track the progress of the design phase.
Thursday:
On Thursday, the Section Chief collaborates with the Quality team to conduct testing of ELVS prototypes. Using KanBo’s Collaboration feature, the Section Chief adds the Quality team members to the workspace and assigns them tasks for testing. After testing, the Quality team members upload their reports in the Document Folder.
Friday:
On Friday, the Section Chief reviews all the ELVS project-related tasks and documents. Using KanBo’s reporting feature, they create a dashboard to showcase the entire project’s progress, including the current status, delayed tasks, and upcoming deadlines. The Section Chief then schedules a weekly check-in with the entire team to discuss any updates and adjustments.
Conclusion:
Managing a complex project such as ELVS requires effective collaboration and communication among team members. With KanBo, the Section Chief was able to manage the project smoothly and efficiently, ensuring all tasks were completed on time with minimal delays. By following this one-week guide, you too can easily navigate and manage projects with ease using KanBo.
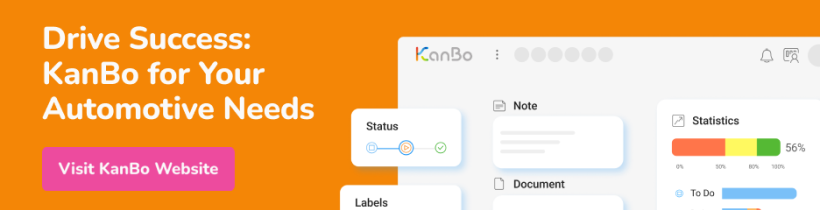
Did you know that KanBo is more than just a tool for Collaboration? It is a comprehensive work management platform that goes beyond simple task tracking and team collaboration. KanBo offers a range of features that make it the go-to platform for large enterprises, from resource management to document management, KanBo can handle it all.
One of the key features of KanBo is its ability to integrate with numerous work applications, including Microsoft Office 365, Google Suite, Salesforce, and AWS. This level of integration allows users to seamlessly access and share data across platforms, leading to improved productivity and streamlined workflow.
Additionally, KanBo’s advanced analytics and reporting tools provide valuable insights into work processes, allowing organizations to identify areas for improvement and optimize efficiency. KanBo’s resource management tools also make it easy to assign tasks and responsibilities, ensuring everyone is working effectively towards the same goal.
Moreover, with KanBo, users can create custom card templates, boards, and workflows that cater to their specific business needs. From HR management to project planning, KanBo can be customized to meet the needs of any type of organization.
In conclusion, KanBo is more than just a collaboration tool; it is a comprehensive work management platform designed for large enterprises. Its diverse range of features, powerful integrations, and customizable workflows make it the go-to platform, aiding in improved productivity, effective collaboration, and streamlined workflow.
Q&A
1. QA: What are some key features of KanBo that make it a useful platform for large enterprises?
A: KanBo offers collaboration tools, automation tools, project planning features, data visualization tools, and document creation support. It has an easy-to-use interface and can be installed both on-premises and in the cloud, catering to the unique needs and preferences of every type of business.
2. QA: How does KanBo support collaboration and alignment across different departments in an enterprise?
A: KanBo brings all teams, departments, and external stakeholders together on a single platform, simplifying communication processes and ensuring alignment in project goals. This leads to more successful project outcomes and improved productivity.
3. QA: How does the use of KanBo benefit the management of the Exterior Lighting and Vision System project?
A: KanBo ensures effective collaboration, task assignment, and progress tracking for the project. The Section Chief can manage all aspects of the project, including task assignment, document creation, progress tracking, and reporting. This helps to ensure that the project is efficiently managed with timely delivery of results.
Use Case: Streamlining Technical Evaluation and Test Procedures in the Automotive Industry with KanBo
One of the key challenges in the automotive industry is coordinating and streamlining the technical evaluation and testing procedures for various parts and components. This process requires rigorous attention to detail and adherence to strict quality standards in order to ensure safety and reliability. However, managing and coordinating these processes can often be complex and time-consuming.
With KanBo, automotive manufacturers can easily streamline their technical evaluation and testing procedures, ensuring quality and consistency of output while minimizing the workload for their teams. Here are some examples of how KanBo can be used in this context:
1. Technical Evaluation Document Template Creation
KanBo can be used to create standardized templates for technical evaluation documents, ensuring consistency across all documents. Templates can be customized to meet specific business needs, with fields for inputting information such as part numbers, specifications, and test results. This makes it easy for teams to create new documents quickly and efficiently.
2. Designing Test Procedures and Standards
KanBo can be used to create and clarify test procedures and standards for various parts and components. This can be done by referencing engineering specifications and customizing them to suit specific business needs. This ensures that all testing is performed according to established standards, minimizing the risk of errors or safety issues.
3. 1st Level Check of Technical Evaluation Documents
Before technical evaluation documents are submitted for approval, they must be thoroughly checked for adherence to DQS standards and other requirements. KanBo can be used to streamline this process, with a designated point of contact responsible for conducting the 1st level check. This ensures that all documents are consistent and meet all necessary standards before being submitted for final approval.
4. Facilitating PreQ Meetings
PreQ meetings are an important part of the technical evaluation process, ensuring that all stakeholders are aligned and informed about upcoming testing requirements. KanBo can be used to schedule and facilitate these meetings, ensuring that all relevant parties are aware of the testing requirements and timelines.
5. Reporting Concerns and Proposing C/Ms
If concerns or issues arise during the technical evaluation process, KanBo can be used to report them to the relevant authorities and propose corrective actions (C/Ms) based on a thorough root cause analysis.
6. Identifying Inefficiencies and Proposing Solutions
KanBo’s advanced analytics and reporting tools can be used to identify inefficiencies in the technical evaluation and testing process and propose solutions to mitigate unnecessary workload and improve downstream impact. This ensures that the testing process is optimized for efficiency and safety, while minimizing the workload for teams.
By using KanBo to streamline technical evaluation and testing procedures, automotive manufacturers can ensure quality, consistency, and safety in their products, while minimizing the workload for their teams. With its easy-to-use interface and customizable features, KanBo is a powerful tool for any organization looking to improve collaboration and efficiency. Best of all, users can easily integrate it with familiar Microsoft Office applications, streamlining workflow and minimizing the learning curve.
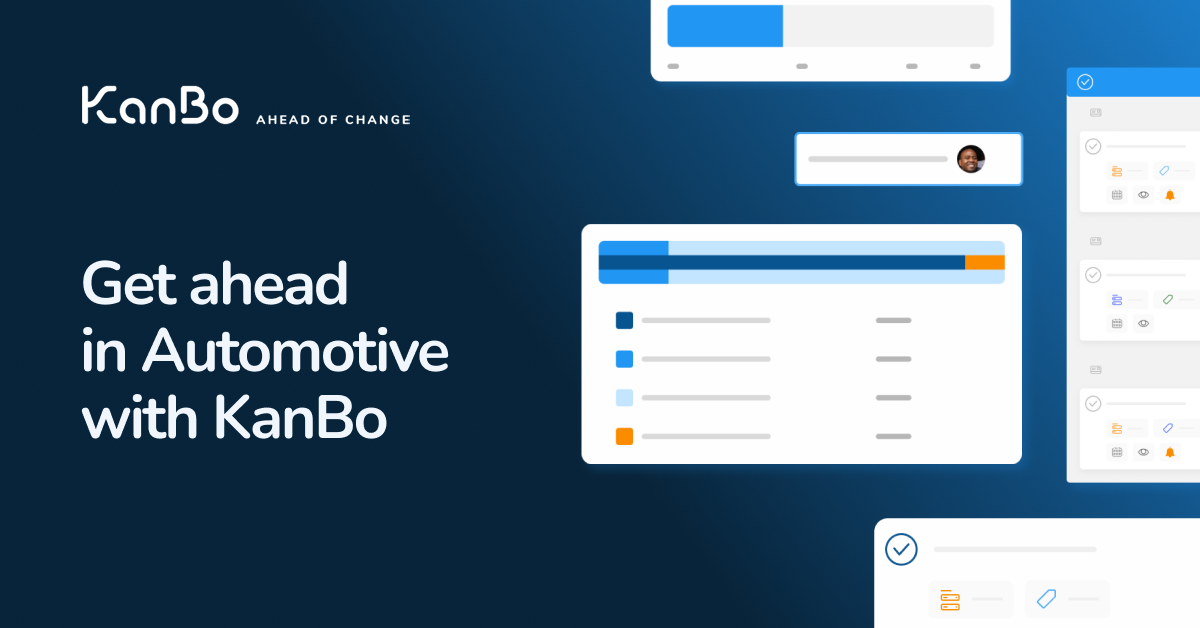