Work coordination platform
Designed for the automotive industry
As a leader in innovation, you understand the importance of staying ahead of the curve in the fast-moving automotive 4.0 world. KanBo provides you with the tools to do just that by facilitating smart factory operations, streamlining project management, fostering collaboration and solving complex problems.
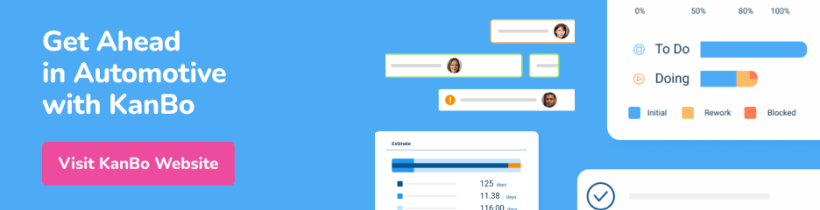
Boosting Collaboration and Quality Control: The Power of KanBo for Group Leaders in Automotive Industry
As the business world continues to evolve, companies need to keep up with the latest technology if they want to stay ahead of the game. For large enterprises, this means having a work coordination platform that can bring together all teams, departments, and external stakeholders. This is where KanBo comes in, a software platform designed to help organizations collaborate effectively, anywhere, anytime.
One of the key advantages of KanBo is its ability to cater to the diverse needs and preferences of businesses. Whether a company prefers on-premises or cloud installations, KanBo can provide the right solution. This flexibility means that businesses can use KanBo regardless of their size, location or industry.
One of the essential use cases for KanBo is in the automotive industry, where KanBo’s collaboration features can enhance the quality control department’s processes. KanBo provides a dedicated Quality Control Test and Analysis Group Leader with the tools to lead, develop, and execute work plans to ensure products produced meet/exceed the set specifications. By using KanBo, the team can create and execute quality hoshin to achieve company KPI.
Moreover, KanBo promotes a strong kaizen culture to ensure continuous improvement. With KanBo, teams can collaborate across different departments, locations, and even time zones. They can closely collaborate with external stakeholders, such as suppliers or dealers, to ensure that their products meet the highest level of quality and customer expectations.
Some of the benefits of implementing KanBo include improved communication, increased productivity, and streamlined workflows. The software’s task assignment feature allows teams to assign tasks to individual team members and track their progress. The document sharing feature enables collaborations on files, contracts or technical drawings that need to comply with strict quality standards.
In summary, KanBo is a work coordination platform designed to help large enterprises collaborate effectively, no matter where they are located. With an emphasis on collaboration, KanBo provides the necessary tools to ensure quality control while fostering a strong company culture. Try KanBo today by accessing their Sandbox demonstration environment, and see for yourself why it is the platform of choice for leading automotive companies.
As a Quality Control Test and Analysis Group Leader in the automotive industry, you know how crucial it is to ensure that every product is of high quality. You need a reliable and efficient system to manage your work and team effectively. KanBo is the perfect solution for that.
Let’s explore how you can use KanBo and collaboration to manage your work effectively for one week, from Monday to Friday.
Monday: Start by creating a KanBo workspace for your team. You can create cards for each task and assign them to the respective team members. Use the Kanban view to visualize the progress of tasks in various stages of completion.
Tuesday: Share documents related to the tasks with the team. Use the document folders and groups to organize and manage the files efficiently. Use the card relations to link related tasks and documents together.
Wednesday: Schedule a card to set a deadline and remind team members of the approaching deadline. Use the Gantt chart view to manage different project timelines effectively.
Thursday: Use the table (spreadsheet) view to analyze and manage numerical data, such as test results. Visualize the data with graphs and charts to identify trends and patterns easily.
Friday: Review the progress of tasks, analyze team performance, and generate reports using KanBo dashboards and data visualization features. Share reports and insights with the team and stakeholders in the automotive industry.
With KanBo and collaboration, you can manage your work and team efficiently, ensure the quality of your products, and stay ahead of the curve in the fast-moving automotive world.
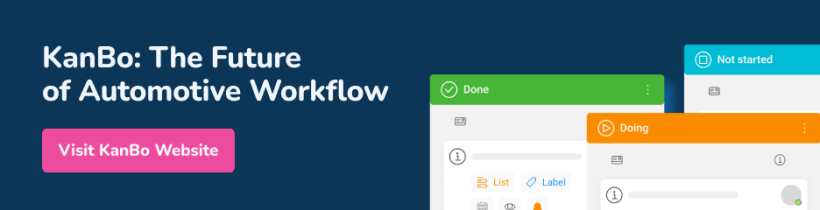
Did you know that KanBo is more than just a tool for collaboration? KanBo is designed to streamline work management and coordination within an organization. Its features allow for efficient allocation of tasks and responsibilities, clear communication, tracking of progress, and analytics. In essence, KanBo is a solution for optimizing work processes, not just collaboration.
With KanBo, users can create customizable workspaces and cards that represent tasks and projects. Assigning tasks to employees and setting deadlines is easy, giving team members more autonomy and clarity in their roles. Additionally, KanBo offers a variety of views, including Kanban, Gantt chart, calendar, timeline, and more, to visualize work and progress. Users can even create reports and dashboards to identify bottlenecks in processes and optimize performance.
KanBo also boasts a range of integrations with other commonly used tools like Microsoft Outlook, Teams, SharePoint, and Google Drive, further improving productivity and efficiency. Its intelligent search function allows users to easily find information within KanBo and linked systems.
Overall, KanBo’s features and philosophy make it a valuable tool beyond just collaboration. Its focus on optimizing work processes and facilitating communication and transparency among team members can lead to increased efficiency, productivity, and employee satisfaction.
Q&A
1. Q: What industries can benefit from using KanBo for collaborative work coordination?
A: KanBo is flexible and can provide solutions for businesses of any size, location, or industry. However, one industry that can benefit from KanBo’s collaborative features is the automotive industry. The software provides tools to execute quality hoshin to achieve company KPIs and promote continuous improvement. Teams can also collaborate across different departments, locations, and with external stakeholders, such as suppliers or dealers, to ensure their products meet high-quality standards and customer expectations.
2. Q: How does KanBo promote team collaboration and communication?
A: KanBo provides collaboration tools such as task assignment, document sharing, and card relations to link related tasks and documents together. Teams can also use the Kanban view to visualize the progress of tasks in various stages of completion, and the table (spreadsheet) view to analyze and manage numerical data. The software’s Gantt chart view enables teams to manage different project timelines effectively. Furthermore, KanBo’s dashboard and data visualization features allow teams to review progress, analyze performance, and generate reports to share with stakeholders.
3. Q: Can KanBo be used for on-premises and cloud installations?
A: Yes, KanBo can cater to the diverse needs and preferences of businesses. The platform is flexible and can provide on-premises or cloud installations, enabling businesses of any size, location, or industry to use the software effectively.
Use Case: Streamlining Supplier Collaboration in Automotive Industry with KanBo
Collaboration with external stakeholders is crucial for the automotive industry to ensure that their products meet the highest level of quality and customer expectations. One of the biggest challenges in supplier collaboration is maintaining a transparent and efficient communication channel. KanBo can help organizations streamline their supplier collaboration processes by providing a centralized platform for communication, document sharing, and task management.
For instance, an automotive company can use KanBo to set up a dedicated workspace for their supply chain team. This workspace can include all relevant suppliers, and documents such as contracts, invoices, and technical drawings. Team members can collaborate in real-time, assign tasks to individual suppliers, monitor their progress, and alert them if deadlines are at risk.
Using KanBo, the supply chain team can also track supplier performance, identify any recurring quality issues, and initiate corrective measures to prevent future defects. To foster a strong kaizen culture, the team can also share knowledge and best practices with suppliers, co-create value, and encourage continuous improvement.
One of the key advantages of using KanBo is its integration with Microsoft Office 365, which means users can work seamlessly on documents within the KanBo platform. This feature makes it simpler for users to leverage their existing Microsoft Office skills and work more productively.
In summary, KanBo can help automotive companies streamline their supplier collaboration processes, ensure quality control, and promote a strong kaizen culture. By providing a centralized platform for communication, task management, and document sharing, KanBo enables organizations to collaborate more effectively, anywhere, anytime.
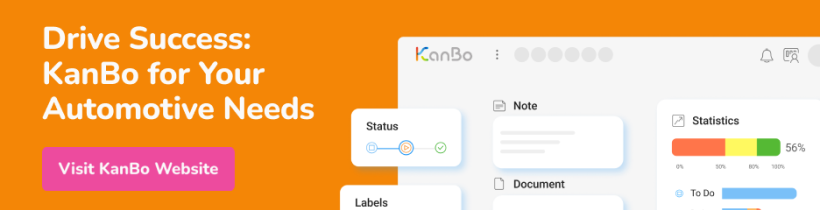